
Combo Roof System
The life of the building could very much depend on the quality and integrity of the roof. The ability of a roof to perform effectively on a long term basis depends on the quality of material,design of the roofing system and quality of workmanship.The extreme heat in the Middle East demands excellent insulation to prevent energy wastage.The Supreme Combo Roofing System does just that, with a saving of over 40% in energy. It also provides for a perfect waterproofing thus making it the ideal and cost effective system. Combo Roof is a comprehensive system comprising of waterproofing,thermal insulation and finishing for the roof.The system is also approved by various authorities like Dubai Municipality, Sharjah Municipality, Sharjah Water and Electricity authority and Trakhees;Combo Roof system is an assured solution for your roof.
Spray foam roofing starts out as two liquid components - Polyfoam / Polyol,known as the "A"component, and a resin (or MDI), the "B" component. When the liquids are mixed at a one-to-one ratio, a chemical reaction occurs and the mixture expands 20 or 30 times forming a solid, monolithic (seamless), closed cell, fully-adhered roof system that provides excellent water-resistance and ther mal insulating abilities. Polyurethane Foam mechanics can spray applies a ta pered roof system with the foam which eliminates the need for costly tapered insulation systems.The vertical wall terminations are also spray applied making them an integral part of the roof system and minimizing additional component costs. Polyurethane foam adheres tojust about everything so it can be installed over concrete,wood, by all major property developers,consultants and contractors.This system provides a manufacturer's Guarantee of 25 years against any leakage. The system meets all latest thermal insulation standards and regulations in UAE and is accepted.
Procedure and Scope of Work
Upon casting and complete curing of roof slab manufacture's engineer shell visit the site to inspect the roof and accept the roof for waterproofing and heat insulation work. A preliminary site inspection shall be carried out and any further preparation work if required shall be brought to the attention of the main contractor. Prior to commencement of roof waterproofing works ,main contractor shell make sure following conditions are met:
All joints existing between roof slab other then expansion joints provided shell be filled with mortar
Rain water outlet shell be place at specified height as per slope.
Vertical parapet wall shell be plastered to required height.
Roof door threshold shell be in place.
AC or water pipe sleeves shell be place at minimum height of 400mm
All other work shall be completed on roof prior to commencement of waterproofing works.
On acceptance of roof from the main contractor, application crew of the approved manufacturer shell visit the site to commence merchandized cleaning operation using compressed air to free the entire substrate from dust and any other loosely laying particles
On completion of cleaning works, other preparatory works shell be under taken like cover ing of parapet wall and other utilities fixed on the roof to avoid risk of over spray
Supply & spray apply of polyurethane over the entire roof area including the up stand to a height of max. 200mm
Supply & Apply of RBE coat over the entire foam area and allow to dry for minimum 25 hours.
Supply & Apply of GEOTEXTILE protection layer over the entire roof area
Supply & lay protective screed in panels and cure as per standard procedures.
Supply & Apply POLYBOND SBR bonding agent to all corners and up stands.
Prepare angle fillet all around parapet skirting area (For foundation- Angle fillet to be done only for direct slab foundation) and up stands using sand cement mortar.
Supply & Apply of POLYSEAL PSPG sealant to all construction joints including backing rod.
Supply & Apply POLYFLEX -COMBO over the entire roof area including up stands and allow drying for 48 hours.
Final inspection shall be carried out and THE MANUFACTURER SHALL ISSUE A LIFETIME GUARANTEE OF 25 YEARS.
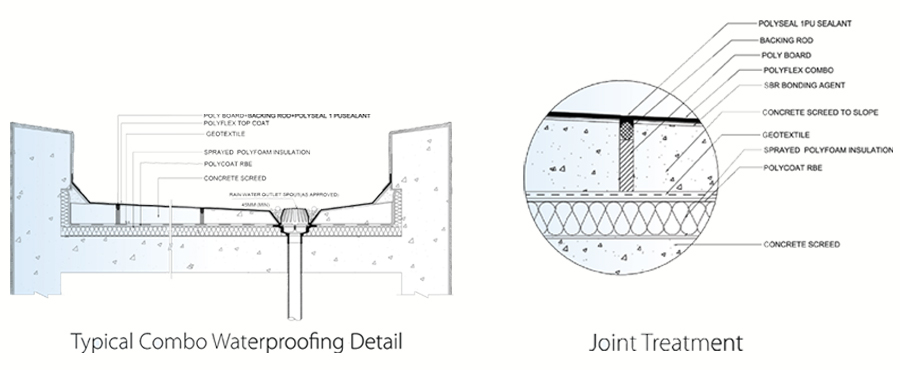

Green Roof Waterproofing
Green Mat - Ideal for Green Roofs
Green Matt is 100% natural . Due to its feature of light weight Green Matt does cause harm or effect various building elements such as building roofs, pillrs and building Foundation Comparatively speaking with other conventional planting methods on roofings that require large volumes of soil.
Environmental Benefits
Green Roofs reduce the Urban Heat Island (UHi) effect the over heating of urban and suburban areas compared to the surrounding country side, due to increased paved, buit-over,and hard surface areas.
Green Roofs can be considered beneficial for their storm water retention capability
Green Roofs can also reduce polution by filtering out dust particulars and other pollutants as the air passes over the plants
Building Benefits
Green Roofs protect buildings from extreme solar radiation, regulate the internal building temperature and decrease the energy required to cool the building
Green roofs help Protect roofing membrane from extreme temprature fluctuations and reduce the nega tive impact of ultraviolet radition
Green Roofs can be used as a sound barrier for the building
Increased out door space or gathering area with fresh air
Green Roofs icrease the asesthetic value of the property
1. Piantation
2. Green Mat 2nd layer
3. Growing media
4. Green Matst layer
5. Sweet soil
6. Geotextile
7. Subsoil modular dra inage
8. layers of water roof
9. Reinforcement concrete

Membrane Waterproofing
Bituminous products are perfect for the water proofing of roofs on buiIdings as they move with the structure as they are not too rigid and do not absorb water. Waterproofing membranes systems are designed to protect both residential and commercial buildings through a mixed substance made up of organic liquids that are highly sticky and viscous and also can be used as a continuous waterproofing membrane for foundations, basements,tunnels, concrete etc. and it is applied by flame bonding. Bituminous membranes are made up of more than one product. Bitumen mixed with a fil ler (limestone or sand) component such as sand. Polymers are added to the bitumen such as APP (Atactic polypropylene) a plastic additive that gives rigidity and tear resistance, or SBS (styrene butadiene styrene a rubber additive that gives more elastic benefits.
Base Products
Polyester,fiberglass,rag fiber (hessian) and paper.These products are bought in roll format and are pulled through the bitumen mixes on huge rollers. The base product becomes saturated in huge tanks by the tar like bitumen substance, creating rolls of waterproof material.
Advantages of this system
Uniform thickness
Membrane can be polyester re-enforced ensuring dimens iona l stability.
Excellent stability at high & low temperatures applications & service
Higher tear & impact resistance & excellent
Ava ilable in plain or mineral finish for light foot traffic.
Process Description
Surface preparation
Surface shall be clea n, dry and free from loose particles
Dust, loose mater ia ls and protrusions must be removed and cracks holes made good.
For better performance surface may be dampened but not wet, particularly in hot and dry weather
Inspection
Prior to start the start of applying primer work the surface shall be inspected and approved by the concern QAQC engineer.
Health & Safety
Protective clothing such as gloves and goggles should be worn when handling the product.Treat any splashes to the skin or eyes with fresh water immediately.
Ensure that the container is available for medical attendant to examine any relevant instructions and content details
Application bituminous primer
Apply by means of brush, roller into the entire coverage area of the substrate and allow drying. The drying time depends on the porosity of the substrate and the environmental conditions (approx.1 .0-3.0 hrs.)

Application bituminous membrane
Bituminous membrane shall be laid fully torched on blinding concrete with minimum of 1OOm end laps and 1SOmm side laps
Waterproofing membrane installation shall be performed using cylinder fed propane gas torch, trowel to seal the seams of the membrane and knife for cutting.
The membrane is then placed in the correct torching on position then re-rolled for about half of its length without changing its orientation.
The membrane is then un-rolled again and torched on pressing the melted area against the substrate.
Repeat till the entire length of the membrane is bonded firmly onto the surface then the second membrane is laid in the same way with an overlap of 1SOmm at the end and 1OOmm at the side.
An extra length of minimum 300mm of the horizontal membrane shall be left to carry up the vertical surface to maintain continuity of the membrane and be protected as above.
The membrane on the exposed external vertical surfaces shall be carried up to a minimum of 150 mm above the finished ground level (i.e. side walk, retaining wa ll, columns etc.) and tucked into a continuous groove provided for the same and secured firmly with approved sea lant/mastic recommended by the manufacturer of the membrane.
Inspection would be submitted for approval
of the Engineer. and tucked into a continuous groove provided for the same and secured firmly with approved sealant/mastic recommended by the manufacturer of the membrane.
Inspection would be submitted for approval of the Engineer.

Technical Detail For Roof Area


Technical Detail For Substructure Area


GRP Lining Waterproofing
GRP lining is a hose relining method in which the inliner used is a seamless glass fibre fabric hose. GRP lining can be used to rehabilitate sewers with damage such as root penetration, depos its,socket offset,cracks and pipe fractures. Once the existing pipe has been cleaned and inspected by a camera, it is prepared for rehabilitation with milling and smoothing robots, which pulls the folded in liner hose into the existing pipe through a shaft. When subjected to compressed air the in liner unfolds and applies itself to the inside wall of the existing pipe.The curing method is selected according to site conditions - using either ultraviolet light or a mixture of air and steam. Unsaturated polyester resins or vinylester resins are used, depending on the level of exposure to chemicals. The curing process is continuously monitored and recorded with the help of automated devices.

Details of Raw Materials for GRP Lining
Glass Fiber - Chopped Strand Mat (CSM)
Resin - Orthophalic Polyester Resin NCS 985 PA
Catalyst - Norpol MEKP
Process Description Grinding
After concreting many irregularities on the surface remain and lamination is carried out on such surface finishing on the outer surface will be inferior. Hence, surface grinding of concrete has to be done, if necessary. This removes all irregularities and the surface becomes clean Moreover,the grinded surface has more porosity which will ensure a stronger bonding with resin.
Dust Removal
After grinding, concrete powder and debris accumulate and this has to be removed as it gets entrapped between the lining and the surface. Hence, the concrete surface is to be cleaned properly with acetone and it is ensured that no impurities are entrapped
GRP lining is a hose relining method in which the inliner used is a seamless glass fibre fabric hose. GRP lining can be used to rehabilitate sewers with damage such as root penet ration, deposits, socket offset, cracks and pipe fractures.
Once the existing pipe has been cleaned and inspected by a camera,it is prepared for rehabilitation with milling and smoothing robots,which pulls the folded in liner hose into the existing pipe through a shaft. When subjec ted to compressed air the in liner unfolds and applies itse lf to the inside wa ll of the existing pipe. The curing method is selected according to site conditions - using either ultraviolet light or a mixture of air and steam. Unsaturated
polyester resins or vinyl ester resins are used, depending on the level of exposure to chemicals. The curing process is continuously monitored and recorded with the help of automated devices.
.
Process Description
Grinding
After concreting many irregularities on the surface remain and lamination is carried out on such surface finishing on the outer surface will be inferior. Hence, surface grinding of concrete has to be done, if necessary.This removes all irregularities and the surface becomes clean Moreover,the grinded surface has more porosity which will ensure a stronger bonding with resin.
Dust Removal
After grinding, concrete powder and debris accumulate and this has to be removed as it gets entrapped between the lining and the surface. Hence, the concrete surface is to be cleaned properly with acetone and it is ensured that no impurities are entrapped
Lamination
Process of lamination for open areas of benching:
After the surface preparation and removal of dust,first coat of resin is applied on the concrete surface. Care is taken to see that the resin fills all voids in the concrete surface so as to avoid the formation of air bubbles.
One coat resin is applied on concrete surface.Then first pre-tra iled layer of glass fiber (CSM) is placed on the resin applied surface.
A woolen roller is used for applying the resin on the mat.
Second layer of glass fiber (CSM) is placed over the first layer with resin applied over it.
Metallic roller is used to impregnate the lamination and to remove any air entrapment.
Sufficient time is allowed for successive glass fiber impregnation to avoid peak exothermic heat.
Successive layer is applied on the a lready impregnated lamination with thickness condition for better bonding between the layers.The procedure is repeated until required thickness is achieved.
Finally top coat will be applied on the cured lamination

Wet Areas Waterproofing
Waterproofing of wet areas such as toilets, bathrooms, kitchens and balconies is critical on account of the constant use of water. The points of leakages are weak areas such as wall joints, joints between cisterns and pipes and faulty piping materials that corrode. If the moisture spreads through the floor or walls to the concrete, it can cause extensive damage to the rebars embedded in the concrete. Thus, it is important to have an impermeable barrier over the concrete to prevent the spread of moisture. We offer a specially designed system for all kinds of wet areas: bathrooms, kitchens or toilets. These are acrylic-based elastomeric coatings, which protect wet areas from constantly occurring water leakages.
wet areas key features:
• Higher waterproofing protection:
Redx systems, with their two component polymer flexible mortar waterproofing slurry, are especially designed for ensuring an unfaultable protection against moisture penetration. All corners, joints, edges, floor drains and pipe penetrations are sealed, for maximum efficiency and durability.
• Micro-bacterial & crack protection:
The flexible and water-repellent components of Redx systems, enable a higher protection
against the usual micro-bacterial organisms which can develop in all moisture exposed areas and
in the same time, ensure a better cracking resistance, for a healthier environment and a more aesthetical appearance.
• Easy & fast application:
The superior workability and easy application features that come along with the products comprised
by our Redx systems, lead to a faster application process, thus a significant time saving
booster.

Light Weight Foam Concrete Service
Foam concrete is a type of porous concrete. According to its features and uses it is similar to concrete.The synonyms are:
• Aerated concrete
• Lightweight foam concrete
• Porous concrete
Foam concrete is created by uniform distribution of air bubbles throughout the mass of concrete. Foam concrete is produced by mechanical mixing of foam prepared in advance with concrete mixture, and not with the help of chemical reactions. Foam is prepared in special device - foam generator and after that mixing in special mixer. (For example machine Foam-Prof consist from special mixer and foam generator mounting toget her). Foam Concrete is normal concrete with bubbles of air inside.Therefore it has the same characteristics with many additional advantages. Also CLC can be produced and poured for floors and roofs on-site. In roofs it can be used because of very good insulating and lightweight. For floors CLC offers faster installation and a less expensive option because of the flowing and self-leveling properties.

Pile Head Treatment Systems
A pile cap is a thick concrete mat that rests on concrete or timber piles that have been driven into soft or unstable ground to provide a suitable stable foundation. It usually forms part of the foundation of a building, typically a multi-storey building, structure or support base for heavy equipment.The cast concrete pile cap distributes the load of the building into the piles. A similar structure to a pile cap is a 'raft':whic h is a concrete foundation floor resting directly onto soft soil which may be liable to subsidence.
The Adva ntage of Pile Head/Cap Treatment :
The Pile Head Treatment is the final working step of a successful piling and foundation system. Every pile has to be protected against chloride and sulphate attacks on the reinforcement caused by the soil and groundwater. It a lso has to assure that there will be no passage of water from the ground to the substructure. A proper designed system shall include: Re-profiling, water proofing and full encapsulation of the entire pile head to assure that each and every structure is based on a long lasting and safely built foundation.

Warehouse & Metal Roofing System
A metal roof, often refer red to as a tin roof, is a roofing system made from metal pieces or tiles. It is a component of the building envelope and often used to cover large buildings beca use of their high strength to weight ratio
Metal sheet roofs are very affordable, durable, and quick to install, which makes their use extremely popular in the construction of commercial and industrial buildings. The major problem with metal roofs in warm weather is that they absorb and retain enormous quantities of heat. In non-air-conditioned buildings, this translates direct ly into high building envelope heat loads, temperature and moisture build-up. In air-conditioned buildings, it means higher energy costs as the air-conditioning has to fight the heat that builds up during the day, even when the sky is overcast (ult raviolet rays, the major source of heat from solar radiation, will penetrate clouds). Because buildings with metal roofs are hotter tha n the things around them,they contribute to the urban heat island effect A metal sheet roof in tropical countries, for example, can reach a temperature above 75 oc I 167 of and the second major problem is the leakage throughout the seams and joints will cause serious deterioration, rust, corrosion and severe structural damage.

Cementitious & Fibrated Waterproofing
Cementations systems generally are available as ready to apply. The two components systems consist of a resin base which is normally an acrylic co-polymer with water proofing properties and a cementations powered roller or by spray . A fabric scrim we suggested over expansion joints to protect the layer from tensile thermal expansion on the roof. Cementations systems are also applied over spray applied polyurethane thermal insulation as a protective layer, as these systems possess high resistanceto UVrays. Since application skills requireare minimum, they highly popular among maintenance contractors. However, it should be noted that the water proofing and durability membrane and care should be exercised in choosing one with adequate co-polymer content.

Water Tanks & Swimming Pools
When constructing a new water tank or swimming pool, it is possible to apply the waterproofing system to the internal (negative) or external (positive) side of the wall. In many cases,combined systems are specified to provide enhanced protection.
Our clients can ava il from us water tanks & swimming pools water proofing services. These services help in enhancing the life of the water tanks/swimmi ng pools by avoiding water from damaging the walls. Our skilled wor kers perform two chemical coat systems with fiber mesh on the tanks/swimming pools. The coating done is highly insoluble in the water. These services are accomplished in less time period and come with a warranty of five years.
Recommended used materials:
• Cementatious Coating
• Crysta lline Coating
• Epoxy Polysulfide Coating

Thermal Insulation Service
The accelerated constructiona l activities coupled with the ever increasing demand for economical and comfortable living encourages us to adopt the latest scientific and technology advancements. Hence we have chosen the concept of the Thermal Insulation system, which plays a vital role in improving the cooling conditions inside buildings. This definitely reflects on power consumption and money involved for all parties concerned in the construction process.
Thermal Insulation System has been introduced to reduce your electric consumption costs up to 40%,thus saving money and the country's energy resources. It a lso indeed creates a more comfortable living and wor king atmosphere.

Injection Treatment
All materials whet her loose or on pallets have to be stored in a covered area and protected from UV and sunlight. Damage to the material may be caused due to improper storage and at high temperatures. Application of materials should be avoided in case of extreme weather conditions like sand storm or rain. The ambient temperature during application should be between S°C and 45°C.
Process Description
Surface Requirements
Drill the hole adjacent to the crack in 45° angle & adjacent to the pipe penetration In the presence of running water the flow must be stopped using POLYINJECT STOP or POLYINJECT STOP FS which produces rapid setting water-stopping foam. When the water is stopped the cracks are re-injected with POLYINJECT PU+.
Work Preparations
POLYINJECT PU+ is applied as injection resin with using injection packers and 1-C pumps.The injection packers may be fixed into holes drilled directly into the crack or drilled diagonally from concrete adjacent to the crack or by fixing of injection nipples bonded to the surface using POLYPUR F on damp surfaces or POLYPOXY BF on dry surfaces. For further assistance and instructions regarding the packer fixing and design please refer to our method statement
Mixing
Pour the hardener (component B) into the resin (component A) in the indicated mixing ratio and mix with an electrical mixer (max. 300 rpm) until a homogenous mixture is produced. Assure that the B component is evenly dispersed. Only mix sufficient resin that can be used within the pot life of the material
Injection
POLYINJECT PU+ can be injected with using 1-component or 2-component injection pumps. The injection pressure should be at least 4 bars. After the wor k is finished the injection system shall be a llowed to cure for 24 hours and shall be left undisturbed for this time.
Cleaning
Remove the packers once POLYI NJECT PU+ is fully cured and make good any holes or voids with POLYPOXY BF on dry surfaces and a llow curing. In case of damp surfaces use POLYPUR F. POLYINJECT PU+, POLYPOXY BF and POLYPU R F should be removed from tools, equipment and mixers with an appropriate solvent immediately after use. Hardened material can only be removed mechanicaIly.
